YN-A750 Reactive Bonding Polymer Self-Adhesive Waterproof Membrane
Product Overview
YN-A750 Reactive Bonding Polymer Self-Adhesive Waterproof Membrane is a self-adhesive polymer membrane-based waterproof material made of polyester film as the reinforcing material, polymer-modified asphalt containing active additives as the coating material, and anti-stick isolation materials covering both the top and bottom surfaces.
During installation, this membrane employs the wet laying method, allowing the pressure-sensitive reactive adhesive of the membrane to crosslink and engage with the cement gel, thereby forming a fully adhered waterproof layer that prevents water leakage.
Product Features
-
Strong Bonding Force: This material can bond with the concrete substrate through a synergistic combination of chemical and physical reactions.
-
Excellent Self-Healing and Local Self-Locking Water Resistance: The high-quality self-adhesive layer has good self-healing properties and can react with cement gel to form an interfacial sealing layer, preventing water leakage.
-
Good Elongation and Tensile Strength: It adapts to deformations in the structural substrate and can self-heal in case of damage (with hole diameters below 2mm).
-
Self-Locking at Leak Points: In the event of leakage, it can self-lock and prevent diffusion, facilitating maintenance.
-
Displacement Capability of Self-Adhesive Glue: It has good adaptability to deformations or cracks in local structures.
-
Flexible Material and Easy Installation: The material is flexible, and the installation process is simple, making it suitable for various complex substrate surfaces.
Waterproofing Principle
The "calcium silicate gel" added to the self-adhesive glue coating on the surface of the membrane causes hydration on the surface of the creep self-adhesive layer to produce gel, which reacts with cement to form hydrated gel. These reactants mutually penetrate to form an interpenetrating polymer network (IPN) structure, thereby firmly adhering the waterproof layer of the membrane to the surface of the structural concrete. This waterproofing mechanism is based on the "skin-type" waterproofing concept.
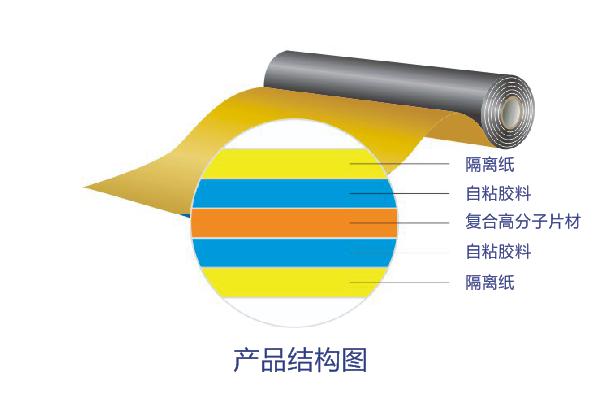
Scope of Application
- Waterproofing and impermeability for various underground projects, such as basements, subways, tunnels, and other waterproofing works;
- Roof waterproofing for industrial and civil buildings;
- Waterproofing works for underground garage roofs, rooftop gardens, and other similar projects;
- Waterproofing works for fire protection ponds.
Key Construction Points
-
Base Layer Cleaning and Wetting: Use brooms, shovels, and other tools to clean dust and debris from the surface of the base layer. A dry base layer should be pre-wetted with water but should not have ponding.
-
Polymer Cement Mortar: When using polymer cement waterproof mortar, its thickness is generally 2mm-3mm. When applying the mortar, care should be taken to compact and smooth it out. At internal corners, a rounded corner with a radius of 50mm should be formed with cement mortar during base layer preparation. The width of the polymer cement mortar should be wider than the length of the waterproof membrane, with an additional width of 100mm-300mm on each short side of the membrane, and the flatness of the polymer cement mortar should be ensured.
-
Reinforcement of Detailed Nodes: Before laying large areas of waterproof membrane, reinforcement should be applied to detailed node areas as required by specifications.
-
Laying of Large Areas of Waterproof Membrane: Remove the release material on the lower surface of the waterproof membrane and lay it flat on the polymer cement mortar. Adjacent membranes should be laid in a parallel lap joint manner (generally, butt joints are not recommended). The width of the lap joint should be no less than 80mm.
-
Mortar Extraction and Air Ventilation: Use a wooden trowel or rubber plate to tap the upper surface of the membrane to vent air underneath and ensure tight bonding between the membrane and the polymer cement mortar.
-
Curing: After laying the waterproof membrane, it should be cured for 48 hours (the specific time depends on the ambient temperature; generally, higher temperatures require shorter curing times).
Construction Process
Base layer preparation → Node treatment → Positioning and snapping lines → Preliminary laying of waterproof membrane → Application of cement mortar → Laying of waterproof membrane → Lap joint and edge treatment → Rolling, pressing, and ventilation → End protection
Specification and Model
Width: 1.0m;
Thickness: 1.5mm, 2.0mm;
Length: 25m, 20m, 15m;
Note: Other specifications and dimensions can be determined through negotiation between the supplier and the buyer.
Technical Specifications
Execution Standard: GB/T 35467-2017 (Category H)
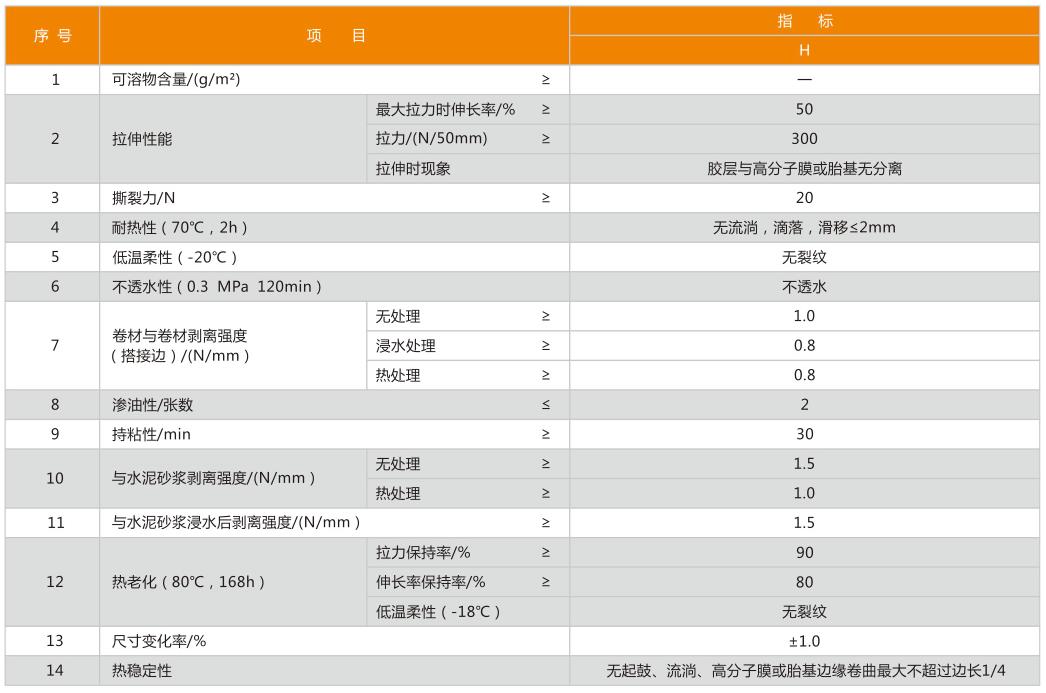